Công nghệ cắt wafer, một bước quan trọng trong quy trình sản xuất chất bán dẫn, có liên quan trực tiếp đến hiệu suất, năng suất và chi phí sản xuất chip.
#01 Bối cảnh và ý nghĩa của việc cắt lát wafer
1.1 Định nghĩa của Wafer Dicing
Cắt wafer (còn được gọi là khắc) là một bước thiết yếu trong sản xuất chất bán dẫn, nhằm mục đích chia các wafer đã xử lý thành nhiều khuôn riêng lẻ. Các khuôn này thường chứa chức năng mạch hoàn chỉnh và là các thành phần cốt lõi cuối cùng được sử dụng trong sản xuất các thiết bị điện tử. Khi thiết kế chip trở nên phức tạp hơn và kích thước tiếp tục thu nhỏ, các yêu cầu về độ chính xác và hiệu quả đối với công nghệ cắt wafer ngày càng trở nên nghiêm ngặt hơn.
Trong các hoạt động thực tế, cắt lát wafer thường sử dụng các công cụ có độ chính xác cao như lưỡi cắt kim cương để đảm bảo mỗi khuôn vẫn còn nguyên vẹn và hoạt động đầy đủ. Các bước chính bao gồm chuẩn bị trước khi cắt, kiểm soát chính xác trong quá trình cắt và kiểm tra chất lượng sau khi cắt.
Trước khi cắt, wafer phải được đánh dấu và định vị để đảm bảo đường cắt chính xác. Trong quá trình cắt, các thông số như áp suất và tốc độ của dụng cụ phải được kiểm soát chặt chẽ để tránh làm hỏng wafer. Sau khi cắt, các cuộc kiểm tra chất lượng toàn diện được tiến hành để đảm bảo rằng mọi chip đều đáp ứng các tiêu chuẩn hiệu suất.
Các nguyên tắc cơ bản của công nghệ cắt wafer không chỉ bao gồm việc lựa chọn thiết bị cắt và thiết lập các thông số quy trình mà còn bao gồm ảnh hưởng của các đặc tính cơ học và đặc điểm của vật liệu đến chất lượng cắt. Ví dụ, wafer silicon điện môi k thấp, do các đặc tính cơ học kém hơn, rất dễ bị tập trung ứng suất trong quá trình cắt, dẫn đến các hỏng hóc như mẻ và nứt. Độ cứng và độ giòn thấp của vật liệu k thấp khiến chúng dễ bị hư hỏng cấu trúc hơn dưới tác động của lực cơ học hoặc ứng suất nhiệt, đặc biệt là trong quá trình cắt. Tiếp xúc giữa dụng cụ và bề mặt wafer, cùng với nhiệt độ cao, có thể làm trầm trọng thêm sự tập trung ứng suất.
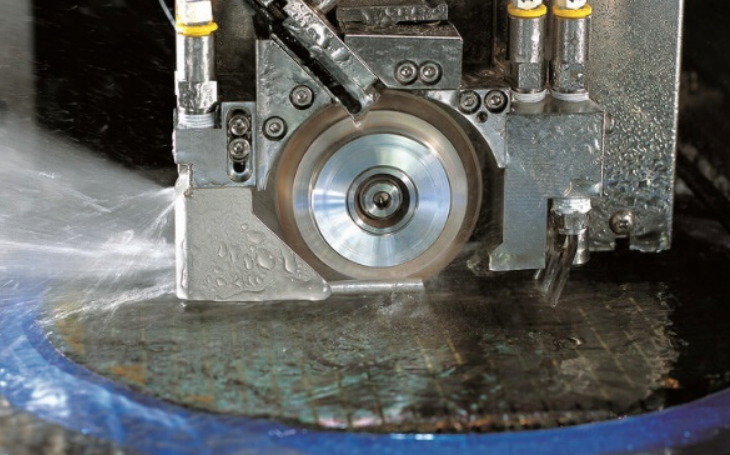
Với những tiến bộ trong khoa học vật liệu, công nghệ cắt lát wafer đã mở rộng ra ngoài các chất bán dẫn gốc silicon truyền thống để bao gồm các vật liệu mới như gali nitride (GaN). Những vật liệu mới này, do độ cứng và đặc tính cấu trúc của chúng, đặt ra những thách thức mới cho các quy trình cắt lát, đòi hỏi phải cải tiến hơn nữa về công cụ và kỹ thuật cắt.
Là một quy trình quan trọng trong ngành công nghiệp bán dẫn, việc cắt wafer tiếp tục được tối ưu hóa để đáp ứng nhu cầu ngày càng tăng và những tiến bộ công nghệ, đặt nền tảng cho công nghệ vi điện tử và mạch tích hợp trong tương lai.
Những cải tiến trong công nghệ cắt lát wafer không chỉ dừng lại ở việc phát triển các vật liệu và công cụ phụ trợ. Chúng còn bao gồm tối ưu hóa quy trình, cải tiến hiệu suất thiết bị và kiểm soát chính xác các thông số cắt lát. Những tiến bộ này nhằm mục đích đảm bảo độ chính xác, hiệu quả và tính ổn định cao trong quy trình cắt lát wafer, đáp ứng nhu cầu của ngành công nghiệp bán dẫn về kích thước nhỏ hơn, tích hợp cao hơn và cấu trúc chip phức tạp hơn.
Khu vực cải tiến | Các biện pháp cụ thể | Các hiệu ứng |
Tối ưu hóa quy trình | - Cải thiện khâu chuẩn bị ban đầu, chẳng hạn như định vị wafer và lập kế hoạch đường đi chính xác hơn. | - Giảm lỗi cắt và cải thiện độ ổn định. |
- Giảm thiểu lỗi cắt và tăng cường độ ổn định. | - Áp dụng cơ chế giám sát và phản hồi thời gian thực để điều chỉnh áp suất, tốc độ và nhiệt độ của dụng cụ. | |
- Giảm tỷ lệ vỡ wafer và cải thiện chất lượng chip. | ||
Nâng cao hiệu suất thiết bị | - Sử dụng hệ thống cơ khí có độ chính xác cao và công nghệ điều khiển tự động tiên tiến. | - Nâng cao độ chính xác khi cắt và giảm lãng phí vật liệu. |
- Giới thiệu công nghệ cắt laser phù hợp với vật liệu có độ cứng cao. | - Nâng cao hiệu quả sản xuất và giảm thiểu sai sót thủ công. | |
- Tăng cường tự động hóa thiết bị để giám sát và điều chỉnh tự động. | ||
Kiểm soát tham số chính xác | - Điều chỉnh chính xác các thông số như độ sâu cắt, tốc độ, loại dụng cụ và phương pháp làm mát. | - Đảm bảo tính toàn vẹn của khuôn và hiệu suất điện. |
- Tùy chỉnh các thông số dựa trên vật liệu, độ dày và cấu trúc của wafer. | - Tăng tỷ lệ năng suất, giảm lãng phí vật liệu và giảm chi phí sản xuất. | |
Ý nghĩa chiến lược | - Không ngừng khám phá những con đường công nghệ mới, tối ưu hóa quy trình và nâng cao năng lực thiết bị để đáp ứng nhu cầu thị trường. | - Nâng cao năng suất và hiệu suất sản xuất chip, hỗ trợ phát triển vật liệu mới và thiết kế chip tiên tiến. |
1.2 Tầm quan trọng của việc cắt lát bánh wafer
Cắt wafer đóng vai trò quan trọng trong quá trình sản xuất chất bán dẫn, tác động trực tiếp đến các bước tiếp theo cũng như chất lượng và hiệu suất của sản phẩm cuối cùng. Tầm quan trọng của nó có thể được trình bày chi tiết như sau:
Đầu tiên, độ chính xác và tính nhất quán của việc cắt hạt là chìa khóa để đảm bảo năng suất và độ tin cậy của chip. Trong quá trình sản xuất, các tấm wafer trải qua nhiều bước xử lý để tạo thành nhiều cấu trúc mạch phức tạp, phải được chia chính xác thành từng chip (khuôn). Nếu có lỗi đáng kể trong việc căn chỉnh hoặc cắt trong quá trình cắt hạt, các mạch có thể bị hỏng, ảnh hưởng đến chức năng và độ tin cậy của chip. Do đó, công nghệ cắt hạt có độ chính xác cao không chỉ đảm bảo tính toàn vẹn của từng chip mà còn ngăn ngừa hư hỏng cho các mạch bên trong, cải thiện tỷ lệ năng suất chung.
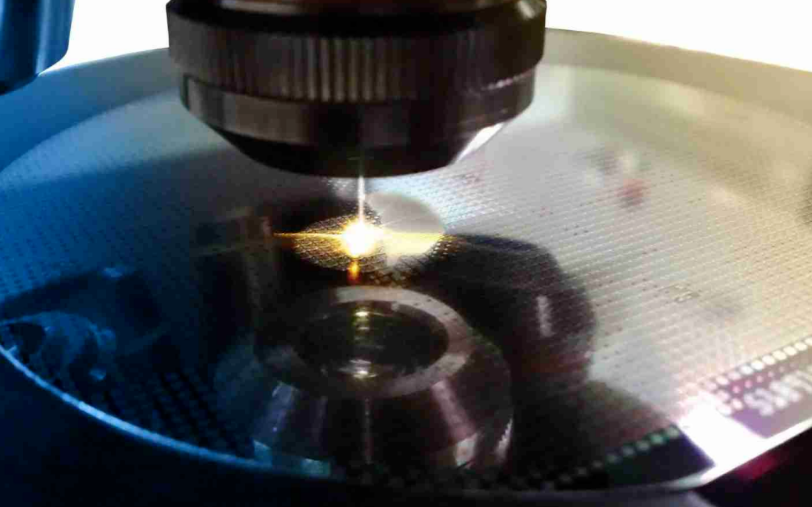
Thứ hai, cắt lát wafer có tác động đáng kể đến hiệu quả sản xuất và kiểm soát chi phí. Là một bước quan trọng trong quy trình sản xuất, hiệu quả của nó ảnh hưởng trực tiếp đến tiến độ của các bước tiếp theo. Bằng cách tối ưu hóa quy trình cắt lát, tăng mức độ tự động hóa và cải thiện tốc độ cắt, hiệu quả sản xuất chung có thể được nâng cao đáng kể.
Mặt khác, lãng phí vật liệu trong quá trình cắt hạt lựu là một yếu tố quan trọng trong quản lý chi phí. Sử dụng công nghệ cắt hạt lựu tiên tiến không chỉ làm giảm tổn thất vật liệu không cần thiết trong quá trình cắt mà còn tăng khả năng sử dụng wafer, do đó làm giảm chi phí sản xuất.
Với những tiến bộ trong công nghệ bán dẫn, đường kính wafer tiếp tục tăng và mật độ mạch cũng tăng theo, đặt ra những yêu cầu cao hơn đối với công nghệ cắt lát. Các wafer lớn hơn đòi hỏi phải kiểm soát chính xác hơn các đường cắt, đặc biệt là ở các khu vực mạch có mật độ cao, nơi mà ngay cả những sai lệch nhỏ cũng có thể khiến nhiều chip bị lỗi. Ngoài ra, các wafer lớn hơn liên quan đến nhiều đường cắt hơn và các bước quy trình phức tạp hơn, đòi hỏi phải cải thiện thêm về độ chính xác, tính nhất quán và hiệu quả của các công nghệ cắt lát để đáp ứng những thách thức này.
1.3 Quy trình cắt wafer
Quy trình cắt lát wafer bao gồm tất cả các bước từ giai đoạn chuẩn bị đến khâu kiểm tra chất lượng cuối cùng, trong đó mỗi giai đoạn đều quan trọng để đảm bảo chất lượng và hiệu suất của các chip cắt lát. Dưới đây là giải thích chi tiết về từng giai đoạn.
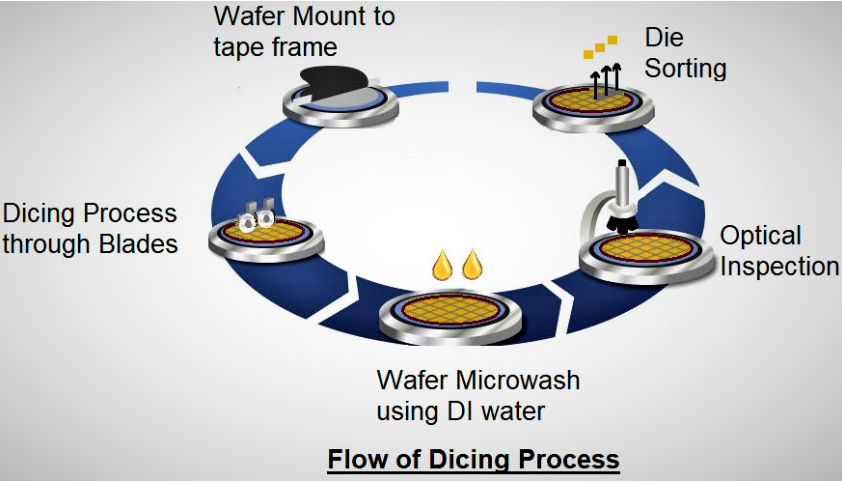
Giai đoạn | Mô tả chi tiết |
Giai đoạn chuẩn bị | -Vệ sinh wafer:Sử dụng nước có độ tinh khiết cao và các chất tẩy rửa chuyên dụng, kết hợp với phương pháp chà siêu âm hoặc cơ học để loại bỏ tạp chất, hạt và chất gây ô nhiễm, đảm bảo bề mặt sạch sẽ. -Định vị chính xác:Sử dụng thiết bị có độ chính xác cao để đảm bảo wafer được chia chính xác dọc theo các đường cắt đã thiết kế. -Cố định wafer: Cố định tấm wafer vào khung băng để duy trì sự ổn định trong quá trình cắt, tránh hư hỏng do rung động hoặc chuyển động. |
Giai đoạn cắt | -Lưỡi dao thái hạt lựu:Sử dụng lưỡi dao phủ kim cương quay tốc độ cao để cắt vật lý, phù hợp với vật liệu gốc silicon và tiết kiệm chi phí. -Cắt bằng tia laser:Sử dụng chùm tia laser năng lượng cao để cắt không tiếp xúc, lý tưởng cho các vật liệu giòn hoặc có độ cứng cao như gali nitride, mang lại độ chính xác cao hơn và ít hao hụt vật liệu hơn. -Công nghệ mới:Giới thiệu công nghệ cắt laser và plasma để cải thiện hiệu quả và độ chính xác hơn nữa đồng thời giảm thiểu vùng ảnh hưởng nhiệt. |
Giai đoạn làm sạch | - Sử dụng nước khử ion (nước DI) và các chất tẩy rửa chuyên dụng, kết hợp với phương pháp làm sạch bằng sóng siêu âm hoặc phun để loại bỏ các mảnh vụn và bụi phát sinh trong quá trình cắt, ngăn ngừa cặn bẩn ảnh hưởng đến các quy trình tiếp theo hoặc hiệu suất điện của chip. - Nước DI có độ tinh khiết cao giúp tránh đưa thêm chất gây ô nhiễm mới, đảm bảo môi trường wafer sạch. |
Giai đoạn kiểm tra | -Kiểm tra quang học:Sử dụng hệ thống phát hiện quang học kết hợp với thuật toán AI để nhanh chóng xác định lỗi, đảm bảo không có vết nứt hoặc sứt mẻ trên các con chip cắt hạt lựu, cải thiện hiệu quả kiểm tra và giảm lỗi của con người. -Đo lường kích thước: Xác minh rằng kích thước chip đáp ứng thông số kỹ thuật thiết kế. -Kiểm tra hiệu suất điện: Đảm bảo hiệu suất điện của các chip quan trọng đạt tiêu chuẩn, đảm bảo độ tin cậy trong các ứng dụng tiếp theo. |
Giai đoạn phân loại | - Sử dụng cánh tay robot hoặc cốc hút chân không để tách các mảnh vụn đạt tiêu chuẩn ra khỏi khung băng và tự động phân loại chúng dựa trên hiệu suất, đảm bảo hiệu quả sản xuất và tính linh hoạt đồng thời cải thiện độ chính xác. |
Quy trình cắt wafer bao gồm làm sạch wafer, định vị, cắt, làm sạch, kiểm tra và phân loại, mỗi bước đều rất quan trọng. Với những tiến bộ trong công nghệ tự động hóa, cắt laser và kiểm tra AI, các hệ thống cắt wafer hiện đại có thể đạt được độ chính xác, tốc độ cao hơn và giảm tổn thất vật liệu. Trong tương lai, các công nghệ cắt mới như laser và plasma sẽ dần thay thế phương pháp cắt lưỡi dao truyền thống để đáp ứng nhu cầu thiết kế chip ngày càng phức tạp, thúc đẩy hơn nữa sự phát triển của các quy trình sản xuất chất bán dẫn.
Công nghệ cắt wafer và nguyên lý của nó
Hình ảnh minh họa ba công nghệ cắt wafer phổ biến:Lưỡi dao thái hạt lựu,Cắt bằng tia laser, VàCắt Plasma. Dưới đây là phân tích chi tiết và giải thích bổ sung về ba kỹ thuật này:
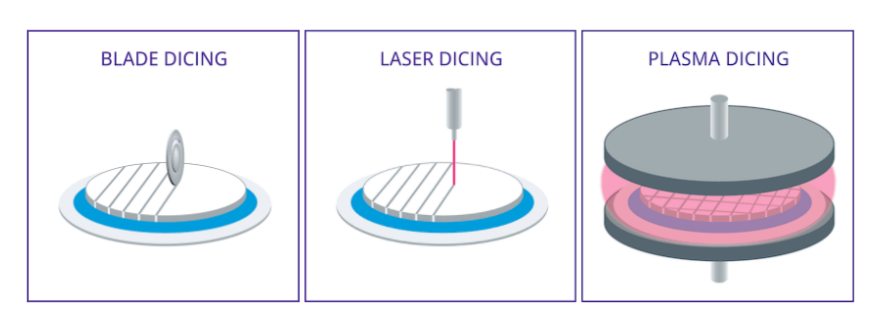
Trong sản xuất chất bán dẫn, cắt wafer là một bước quan trọng đòi hỏi phải lựa chọn phương pháp cắt phù hợp dựa trên độ dày của wafer. Bước đầu tiên là xác định độ dày của wafer. Nếu độ dày wafer vượt quá 100 micron, có thể chọn cắt lưỡi dao làm phương pháp cắt. Nếu cắt lưỡi dao không phù hợp, có thể sử dụng phương pháp cắt gãy, bao gồm cả kỹ thuật cắt vạch và cắt lưỡi dao.
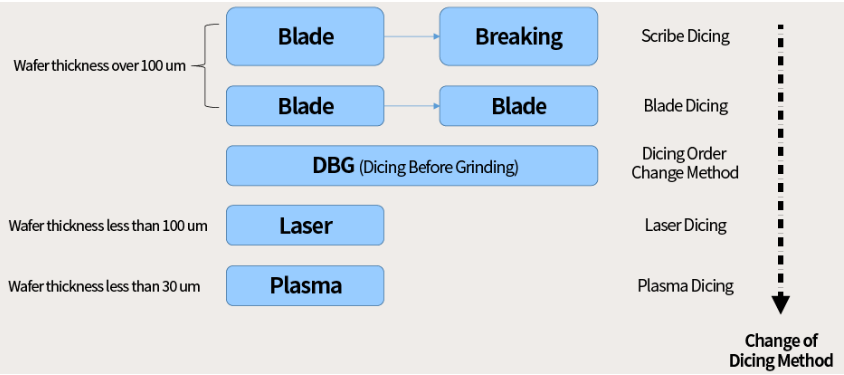
Khi độ dày của wafer nằm trong khoảng từ 30 đến 100 micron, phương pháp DBG (Cắt trước khi mài) được khuyến nghị. Trong trường hợp này, có thể chọn cắt theo đường vạch, cắt lưỡi dao hoặc điều chỉnh trình tự cắt khi cần để đạt được kết quả tốt nhất.
Đối với các wafer siêu mỏng có độ dày dưới 30 micron, cắt laser trở thành phương pháp được ưa chuộng do khả năng cắt wafer mỏng chính xác mà không gây hư hỏng quá mức. Nếu cắt laser không đáp ứng được các yêu cầu cụ thể, cắt plasma có thể được sử dụng thay thế. Sơ đồ này cung cấp một lộ trình ra quyết định rõ ràng để đảm bảo công nghệ cắt wafer phù hợp nhất được lựa chọn trong các điều kiện độ dày khác nhau.
2.1 Công nghệ cắt cơ khí
Công nghệ cắt cơ học là phương pháp truyền thống trong cắt lát wafer. Nguyên lý cốt lõi là sử dụng bánh mài kim cương quay tốc độ cao làm công cụ cắt để cắt lát wafer. Thiết bị chính bao gồm trục chính ổ trục khí, truyền động cho công cụ bánh mài kim cương ở tốc độ cao để thực hiện cắt chính xác hoặc tạo rãnh dọc theo đường cắt được xác định trước. Công nghệ này được sử dụng rộng rãi trong ngành do chi phí thấp, hiệu quả cao và khả năng ứng dụng rộng rãi.
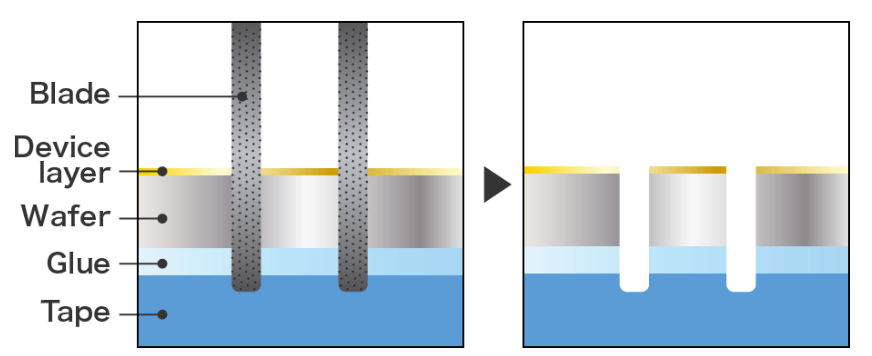
Thuận lợi
Độ cứng và khả năng chống mài mòn cao của dụng cụ mài kim cương cho phép công nghệ cắt cơ học thích ứng với nhu cầu cắt của nhiều loại vật liệu wafer, dù là vật liệu gốc silicon truyền thống hay chất bán dẫn hợp chất mới hơn. Hoạt động của nó đơn giản, với yêu cầu kỹ thuật tương đối thấp, càng thúc đẩy sự phổ biến của nó trong sản xuất hàng loạt. Ngoài ra, so với các phương pháp cắt khác như cắt laser, cắt cơ học có chi phí kiểm soát được hơn, phù hợp với nhu cầu sản xuất khối lượng lớn.
Hạn chế
Mặc dù có nhiều ưu điểm, công nghệ cắt cơ học cũng có những hạn chế. Đầu tiên, do tiếp xúc vật lý giữa dụng cụ và wafer, độ chính xác cắt tương đối hạn chế, thường dẫn đến độ lệch về kích thước có thể ảnh hưởng đến độ chính xác của quá trình đóng gói và thử nghiệm chip sau đó. Thứ hai, các khuyết tật như mẻ và nứt có thể dễ dàng xảy ra trong quá trình cắt cơ học, không chỉ ảnh hưởng đến tỷ lệ năng suất mà còn có thể tác động tiêu cực đến độ tin cậy và tuổi thọ của chip. Thiệt hại do ứng suất cơ học gây ra đặc biệt có hại cho sản xuất chip mật độ cao, đặc biệt là khi cắt vật liệu giòn, khi những vấn đề này nổi bật hơn.
Cải tiến công nghệ
Để khắc phục những hạn chế này, các nhà nghiên cứu liên tục tối ưu hóa quy trình cắt cơ học. Những cải tiến chính bao gồm nâng cao thiết kế và lựa chọn vật liệu của bánh mài để cải thiện độ chính xác và độ bền khi cắt. Ngoài ra, việc tối ưu hóa thiết kế cấu trúc và hệ thống điều khiển của thiết bị cắt đã cải thiện hơn nữa tính ổn định và tự động hóa của quy trình cắt. Những tiến bộ này làm giảm lỗi do thao tác của con người gây ra và cải thiện tính nhất quán của các vết cắt. Việc giới thiệu các công nghệ kiểm tra và kiểm soát chất lượng tiên tiến để theo dõi thời gian thực các bất thường trong quá trình cắt cũng đã cải thiện đáng kể độ tin cậy và năng suất cắt.
Phát triển trong tương lai và công nghệ mới
Mặc dù công nghệ cắt cơ học vẫn giữ vị trí quan trọng trong quá trình cắt wafer, các công nghệ cắt mới đang phát triển nhanh chóng khi các quy trình bán dẫn phát triển. Ví dụ, ứng dụng công nghệ cắt laser nhiệt cung cấp các giải pháp mới cho các vấn đề về độ chính xác và khuyết tật trong quá trình cắt cơ học. Phương pháp cắt không tiếp xúc này làm giảm ứng suất vật lý trên wafer, giảm đáng kể tỷ lệ mẻ và nứt, đặc biệt là khi cắt các vật liệu giòn hơn. Trong tương lai, việc tích hợp công nghệ cắt cơ học với các kỹ thuật cắt mới nổi sẽ cung cấp cho sản xuất bán dẫn nhiều lựa chọn và tính linh hoạt hơn, nâng cao hơn nữa hiệu quả sản xuất và chất lượng chip.
Tóm lại, mặc dù công nghệ cắt cơ học có một số nhược điểm nhất định, nhưng việc cải tiến công nghệ liên tục và tích hợp với các kỹ thuật cắt mới cho phép nó vẫn đóng vai trò quan trọng trong sản xuất chất bán dẫn và duy trì khả năng cạnh tranh trong các quy trình tương lai.
2.2 Công nghệ cắt laser
Công nghệ cắt laser, là một phương pháp mới trong cắt wafer, đã dần nhận được sự chú ý rộng rãi trong ngành công nghiệp bán dẫn do độ chính xác cao, không gây hư hỏng tiếp xúc cơ học và khả năng cắt nhanh. Công nghệ này sử dụng mật độ năng lượng cao và khả năng hội tụ của chùm tia laser để tạo ra một vùng ảnh hưởng nhiệt nhỏ trên bề mặt vật liệu wafer. Khi chùm tia laser được áp dụng vào wafer, ứng suất nhiệt được tạo ra khiến vật liệu bị gãy tại vị trí được chỉ định, đạt được khả năng cắt chính xác.
Ưu điểm của công nghệ cắt laser
• Độ chính xác cao:Khả năng định vị chính xác của chùm tia laser cho phép cắt chính xác ở cấp độ micron hoặc thậm chí nanomet, đáp ứng các yêu cầu của sản xuất mạch tích hợp hiện đại có mật độ cao, độ chính xác cao.
• Không có tiếp xúc cơ học:Cắt laser tránh tiếp xúc vật lý với tấm wafer, ngăn ngừa các vấn đề thường gặp trong quá trình cắt cơ học, chẳng hạn như mẻ và nứt, cải thiện đáng kể tỷ lệ năng suất và độ tin cậy của chip.
• Tốc độ cắt nhanh:Tốc độ cắt laser cao góp phần tăng hiệu quả sản xuất, đặc biệt phù hợp với các tình huống sản xuất tốc độ cao, quy mô lớn.
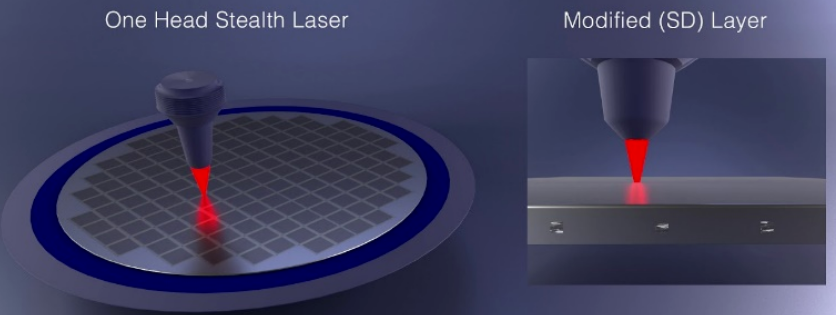
Những thách thức phải đối mặt
• Chi phí thiết bị cao:Đầu tư ban đầu cho thiết bị cắt laser cao, gây áp lực về kinh tế, đặc biệt là đối với các doanh nghiệp sản xuất vừa và nhỏ.
• Kiểm soát quy trình phức tạp:Cắt laser đòi hỏi phải kiểm soát chính xác một số thông số, bao gồm mật độ năng lượng, vị trí tiêu điểm và tốc độ cắt, khiến quá trình này trở nên phức tạp.
• Các vấn đề về vùng bị ảnh hưởng bởi nhiệt:Mặc dù bản chất không tiếp xúc của cắt laser làm giảm hư hỏng cơ học, ứng suất nhiệt do vùng ảnh hưởng nhiệt (HAZ) gây ra có thể tác động tiêu cực đến các đặc tính của vật liệu wafer. Cần tối ưu hóa thêm quy trình để giảm thiểu tác động này.
Hướng cải tiến công nghệ
Để giải quyết những thách thức này, các nhà nghiên cứu đang tập trung vào việc giảm chi phí thiết bị, cải thiện hiệu quả cắt và tối ưu hóa quy trình.
• Hệ thống quang học và laser hiệu quả:Bằng cách phát triển các loại laser hiệu quả hơn và hệ thống quang học tiên tiến, có thể giảm chi phí thiết bị đồng thời nâng cao độ chính xác và tốc độ cắt.
• Tối ưu hóa các thông số quy trình:Nghiên cứu chuyên sâu về tương tác giữa tia laser và vật liệu wafer đang được tiến hành để cải thiện các quy trình giúp giảm vùng ảnh hưởng nhiệt, qua đó cải thiện chất lượng cắt.
• Hệ thống điều khiển thông minh:Sự phát triển của các công nghệ điều khiển thông minh nhằm mục đích tự động hóa và tối ưu hóa quá trình cắt laser, cải thiện tính ổn định và tính nhất quán của nó.
Công nghệ cắt laser đặc biệt hiệu quả trong các tấm wafer siêu mỏng và các tình huống cắt có độ chính xác cao. Khi kích thước wafer tăng lên và mật độ mạch tăng lên, các phương pháp cắt cơ học truyền thống gặp khó khăn trong việc đáp ứng nhu cầu về độ chính xác cao và hiệu quả cao của sản xuất chất bán dẫn hiện đại. Do những lợi thế độc đáo của nó, cắt laser đang trở thành giải pháp được ưa chuộng trong các lĩnh vực này.
Mặc dù công nghệ cắt laser vẫn phải đối mặt với những thách thức như chi phí thiết bị cao và quy trình phức tạp, nhưng những lợi thế độc đáo của nó về độ chính xác cao và hư hỏng không tiếp xúc khiến nó trở thành một hướng phát triển quan trọng trong sản xuất chất bán dẫn. Khi công nghệ laser và hệ thống điều khiển thông minh tiếp tục phát triển, cắt laser dự kiến sẽ cải thiện hơn nữa hiệu quả và chất lượng cắt wafer, thúc đẩy sự phát triển liên tục của ngành công nghiệp bán dẫn.
2.3 Công nghệ cắt Plasma
Công nghệ cắt plasma, là phương pháp cắt wafer mới nổi, đã thu hút được sự chú ý đáng kể trong những năm gần đây. Công nghệ này sử dụng chùm plasma năng lượng cao để cắt wafer chính xác bằng cách kiểm soát năng lượng, tốc độ và đường cắt của chùm plasma, đạt được kết quả cắt tối ưu.
Nguyên lý hoạt động và ưu điểm
Quá trình cắt plasma dựa trên chùm tia plasma nhiệt độ cao, năng lượng cao do thiết bị tạo ra. Chùm tia này có thể làm nóng vật liệu wafer đến điểm nóng chảy hoặc bốc hơi trong thời gian rất ngắn, cho phép cắt nhanh. So với cắt cơ học hoặc cắt laser truyền thống, cắt plasma nhanh hơn và tạo ra vùng ảnh hưởng nhiệt nhỏ hơn, giúp giảm hiệu quả sự xuất hiện của vết nứt và hư hỏng trong quá trình cắt.
Trong các ứng dụng thực tế, công nghệ cắt plasma đặc biệt hiệu quả trong việc xử lý các tấm wafer có hình dạng phức tạp. Chùm tia plasma có thể điều chỉnh và năng lượng cao của nó có thể dễ dàng cắt các tấm wafer có hình dạng không đều với độ chính xác cao. Do đó, trong sản xuất vi điện tử, đặc biệt là trong sản xuất theo yêu cầu và sản xuất hàng loạt nhỏ các chip cao cấp, công nghệ này cho thấy triển vọng lớn trong việc sử dụng rộng rãi.
Thách thức và hạn chế
Mặc dù công nghệ cắt plasma có nhiều ưu điểm nhưng cũng gặp phải một số thách thức.
• Quá trình phức tạp:Quá trình cắt plasma rất phức tạp và đòi hỏi thiết bị có độ chính xác cao và người vận hành có kinh nghiệm để đảm bảođộ chính xác và ổn định khi cắt.
• Kiểm soát môi trường và an toàn:Bản chất nhiệt độ cao, năng lượng cao của chùm tia plasma đòi hỏi các biện pháp kiểm soát môi trường và an toàn nghiêm ngặt, làm tăng tính phức tạp và chi phí triển khai.
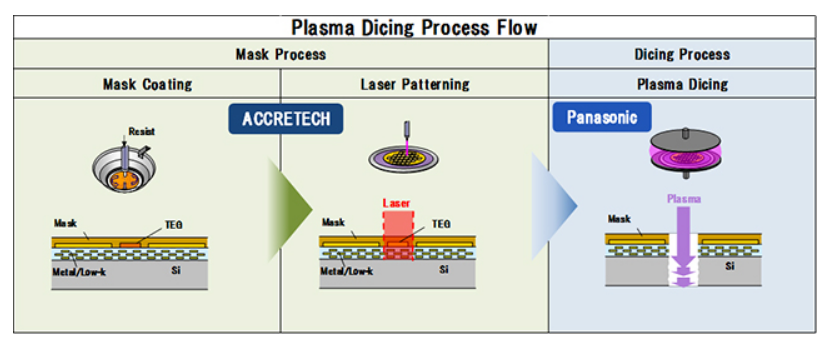
Hướng phát triển trong tương lai
Với những tiến bộ về công nghệ, những thách thức liên quan đến cắt plasma dự kiến sẽ dần được khắc phục. Bằng cách phát triển thiết bị cắt thông minh hơn và ổn định hơn, có thể giảm sự phụ thuộc vào các thao tác thủ công, do đó cải thiện hiệu quả sản xuất. Đồng thời, việc tối ưu hóa các thông số quy trình và môi trường cắt sẽ giúp giảm rủi ro an toàn và chi phí vận hành.
Trong ngành công nghiệp bán dẫn, những cải tiến trong công nghệ cắt và cắt lát wafer đóng vai trò quan trọng trong việc thúc đẩy sự phát triển của ngành. Công nghệ cắt plasma, với độ chính xác cao, hiệu quả và khả năng xử lý các hình dạng wafer phức tạp, đã nổi lên như một công nghệ mới quan trọng trong lĩnh vực này. Mặc dù vẫn còn một số thách thức, những vấn đề này sẽ dần được giải quyết bằng sự đổi mới công nghệ liên tục, mang lại nhiều khả năng và cơ hội hơn cho sản xuất chất bán dẫn.
Triển vọng ứng dụng của công nghệ cắt plasma rất lớn và dự kiến sẽ đóng vai trò quan trọng hơn trong sản xuất chất bán dẫn trong tương lai. Thông qua cải tiến và tối ưu hóa công nghệ liên tục, cắt plasma không chỉ giải quyết những thách thức hiện tại mà còn trở thành động lực mạnh mẽ thúc đẩy sự phát triển của ngành công nghiệp bán dẫn.
2.4 Chất lượng cắt và các yếu tố ảnh hưởng
Chất lượng cắt wafer rất quan trọng đối với việc đóng gói chip, thử nghiệm và hiệu suất chung cũng như độ tin cậy của sản phẩm cuối cùng. Các vấn đề thường gặp trong quá trình cắt bao gồm nứt, mẻ và độ lệch cắt. Những vấn đề này bị ảnh hưởng bởi một số yếu tố kết hợp với nhau.
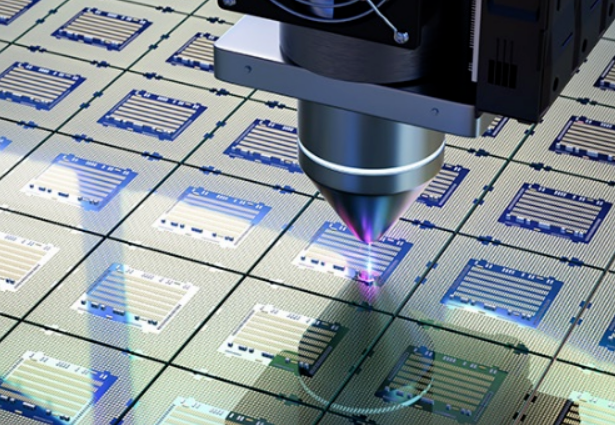
Loại | Nội dung | Sự va chạm |
Các thông số quy trình | Tốc độ cắt, tốc độ nạp liệu và độ sâu cắt ảnh hưởng trực tiếp đến độ ổn định và độ chính xác của quá trình cắt. Cài đặt không đúng có thể dẫn đến tập trung ứng suất và vùng chịu ảnh hưởng nhiệt quá mức, dẫn đến nứt và mẻ. Điều chỉnh các thông số phù hợp dựa trên vật liệu wafer, độ dày và yêu cầu cắt là chìa khóa để đạt được kết quả cắt mong muốn. | Các thông số quy trình phù hợp đảm bảo cắt chính xác và giảm nguy cơ xảy ra khuyết tật như nứt và mẻ. |
Yếu tố thiết bị và vật liệu | -Chất lượng lưỡi dao: Vật liệu, độ cứng và khả năng chống mài mòn của lưỡi dao ảnh hưởng đến độ mịn của quá trình cắt và độ phẳng của bề mặt cắt. Lưỡi dao kém chất lượng làm tăng ma sát và ứng suất nhiệt, có khả năng dẫn đến nứt hoặc mẻ. Việc lựa chọn vật liệu lưỡi dao phù hợp là rất quan trọng. -Hiệu suất làm mát: Chất làm mát giúp giảm nhiệt độ cắt, giảm thiểu ma sát và làm sạch mảnh vụn. Chất làm mát không hiệu quả có thể dẫn đến nhiệt độ cao và tích tụ mảnh vụn, ảnh hưởng đến chất lượng và hiệu quả cắt. Việc lựa chọn chất làm mát hiệu quả và thân thiện với môi trường là rất quan trọng. | Chất lượng lưỡi dao ảnh hưởng đến độ chính xác và độ mịn của vết cắt. Chất làm mát không hiệu quả có thể dẫn đến chất lượng và hiệu quả cắt kém, làm nổi bật nhu cầu sử dụng chất làm mát tối ưu. |
Kiểm soát quy trình và kiểm tra chất lượng | -Kiểm soát quy trình: Theo dõi và điều chỉnh thời gian thực các thông số cắt chính để đảm bảo tính ổn định và nhất quán trong quá trình cắt. -Kiểm tra chất lượng:Kiểm tra ngoại quan sau khi cắt, đo kích thước và thử nghiệm hiệu suất điện giúp xác định và giải quyết kịp thời các vấn đề về chất lượng, cải thiện độ chính xác và tính nhất quán khi cắt. | Kiểm soát quy trình và kiểm tra chất lượng phù hợp giúp đảm bảo kết quả cắt đồng đều, chất lượng cao và phát hiện sớm các vấn đề tiềm ẩn. |

Cải thiện chất lượng cắt
Cải thiện chất lượng cắt đòi hỏi một cách tiếp cận toàn diện có tính đến các thông số quy trình, lựa chọn thiết bị và vật liệu, kiểm soát quy trình và kiểm tra. Bằng cách liên tục tinh chỉnh công nghệ cắt và tối ưu hóa phương pháp quy trình, độ chính xác và độ ổn định của quá trình cắt wafer có thể được nâng cao hơn nữa, cung cấp hỗ trợ kỹ thuật đáng tin cậy hơn cho ngành sản xuất chất bán dẫn.
#03 Xử lý và kiểm tra sau khi cắt
3.1 Vệ sinh và sấy khô
Các bước vệ sinh và sấy khô sau khi cắt wafer rất quan trọng để đảm bảo chất lượng chip và tiến trình diễn ra suôn sẻ của các quy trình tiếp theo. Trong giai đoạn này, điều cần thiết là phải loại bỏ hoàn toàn các mảnh vụn silicon, cặn chất làm mát và các chất gây ô nhiễm khác phát sinh trong quá trình cắt. Điều quan trọng không kém là đảm bảo rằng các chip không bị hư hỏng trong quá trình vệ sinh và sau khi sấy khô, đảm bảo rằng không còn hơi ẩm trên bề mặt chip để ngăn ngừa các vấn đề như ăn mòn hoặc phóng tĩnh điện.
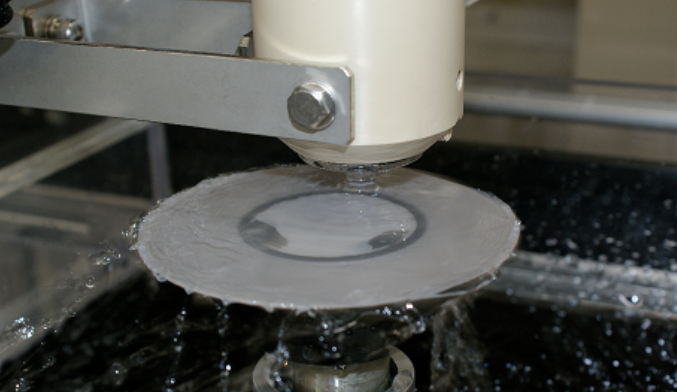
Xử lý sau khi cắt: Quy trình làm sạch và sấy khô
Bước tiến trình | Nội dung | Sự va chạm |
Quy trình vệ sinh | -Phương pháp:Sử dụng chất tẩy rửa chuyên dụng và nước tinh khiết, kết hợp với kỹ thuật chải siêu âm hoặc cơ học để làm sạch. | Đảm bảo loại bỏ hoàn toàn các chất gây ô nhiễm và ngăn ngừa hư hỏng chip trong quá trình vệ sinh. |
-Lựa chọn chất tẩy rửa: Lựa chọn dựa trên vật liệu wafer và loại chất gây ô nhiễm để đảm bảo vệ sinh hiệu quả mà không làm hỏng chip. | Lựa chọn chất tẩy rửa phù hợp là chìa khóa để làm sạch và bảo vệ chip hiệu quả. | |
-Kiểm soát tham số: Kiểm soát chặt chẽ nhiệt độ, thời gian và nồng độ dung dịch vệ sinh để ngăn ngừa các vấn đề về chất lượng do vệ sinh không đúng cách. | Các biện pháp kiểm soát giúp tránh làm hỏng tấm wafer hoặc để lại chất gây ô nhiễm, đảm bảo chất lượng đồng nhất. | |
Quá trình sấy khô | -Phương pháp truyền thống: Sấy khô tự nhiên và sấy khô bằng không khí nóng có hiệu suất thấp và có thể dẫn đến tích tụ tĩnh điện. | Có thể làm thời gian khô chậm hơn và có khả năng xảy ra vấn đề tĩnh điện. |
-Công nghệ hiện đại:Sử dụng các công nghệ tiên tiến như sấy chân không và sấy hồng ngoại để đảm bảo khoai tây chiên khô nhanh và tránh tác hại có hại. | Quá trình sấy nhanh hơn và hiệu quả hơn, giảm nguy cơ phóng tĩnh điện hoặc các vấn đề liên quan đến độ ẩm. | |
Lựa chọn và bảo trì thiết bị | -Lựa chọn thiết bị:Máy làm sạch và sấy khô hiệu suất cao cải thiện hiệu quả xử lý và kiểm soát chặt chẽ các vấn đề tiềm ẩn trong quá trình xử lý. | Máy móc chất lượng cao đảm bảo xử lý tốt hơn và giảm khả năng xảy ra lỗi trong quá trình vệ sinh và sấy khô. |
-Bảo trì thiết bị:Kiểm tra và bảo trì thiết bị thường xuyên để đảm bảo thiết bị luôn ở tình trạng hoạt động tối ưu, đảm bảo chất lượng chip. | Bảo trì đúng cách giúp ngăn ngừa hỏng hóc thiết bị, đảm bảo xử lý đáng tin cậy và chất lượng cao. |
Vệ sinh và sấy khô sau khi cắt
Các bước làm sạch và sấy khô sau khi cắt wafer là các quy trình phức tạp và tinh tế, đòi hỏi phải cân nhắc cẩn thận nhiều yếu tố để đảm bảo kết quả xử lý cuối cùng. Bằng cách sử dụng các phương pháp khoa học và quy trình nghiêm ngặt, có thể đảm bảo rằng mỗi chip đi vào các giai đoạn đóng gói và thử nghiệm tiếp theo trong điều kiện tối ưu.
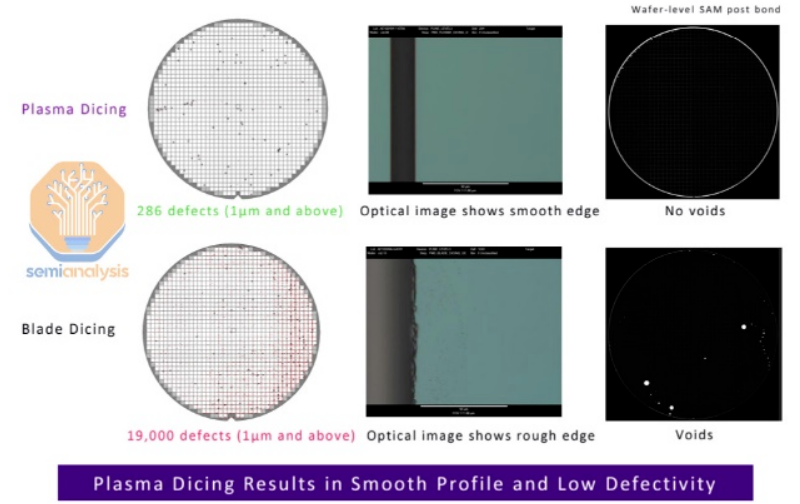
Kiểm tra và thử nghiệm sau khi cắt
Bước chân | Nội dung | Sự va chạm |
Bước kiểm tra | 1.Kiểm tra trực quan: Sử dụng thiết bị kiểm tra trực quan hoặc tự động để kiểm tra các khuyết tật có thể nhìn thấy như vết nứt, mẻ hoặc nhiễm bẩn trên bề mặt chip. Nhanh chóng xác định các chip bị hư hỏng về mặt vật lý để tránh lãng phí. | Giúp xác định và loại bỏ các chip lỗi ngay từ đầu quá trình, giảm thiểu thất thoát vật liệu. |
2.Đo kích thước: Sử dụng thiết bị đo chính xác để đo chính xác kích thước chip, đảm bảo kích thước cắt đáp ứng thông số kỹ thuật thiết kế và ngăn ngừa các vấn đề về hiệu suất hoặc khó khăn trong đóng gói. | Đảm bảo chip nằm trong giới hạn kích thước yêu cầu, ngăn ngừa tình trạng suy giảm hiệu suất hoặc sự cố lắp ráp. | |
3.Kiểm tra hiệu suất điện: Đánh giá các thông số điện chính như điện trở, điện dung và độ tự cảm để xác định chip không đạt tiêu chuẩn và đảm bảo chỉ những chip đạt tiêu chuẩn hiệu suất mới được chuyển sang giai đoạn tiếp theo. | Đảm bảo chỉ những chip có chức năng và hiệu suất đã được kiểm tra mới được tiếp tục tiến hành, giảm nguy cơ hỏng hóc ở các giai đoạn sau. | |
Bước thử nghiệm | 1.Kiểm tra chức năng: Xác minh chức năng cơ bản của chip hoạt động bình thường, xác định và loại bỏ các chip có bất thường về chức năng. | Đảm bảo chip đáp ứng các yêu cầu hoạt động cơ bản trước khi chuyển sang các giai đoạn sau. |
2.Kiểm tra độ tin cậy: Đánh giá độ ổn định hiệu suất của chip khi sử dụng trong thời gian dài hoặc trong môi trường khắc nghiệt, thường bao gồm thử nghiệm lão hóa ở nhiệt độ cao, thử nghiệm ở nhiệt độ thấp và thử nghiệm độ ẩm để mô phỏng các điều kiện khắc nghiệt trong thực tế. | Đảm bảo chip có thể hoạt động đáng tin cậy trong nhiều điều kiện môi trường khác nhau, cải thiện tuổi thọ và độ ổn định của sản phẩm. | |
3.Kiểm tra khả năng tương thích: Xác minh rằng chip hoạt động bình thường với các thành phần hoặc hệ thống khác, đảm bảo không có lỗi hoặc hiệu suất giảm do không tương thích. | Đảm bảo hoạt động trơn tru trong các ứng dụng thực tế bằng cách ngăn ngừa các vấn đề về khả năng tương thích. |
3.3 Đóng gói và lưu trữ
Sau khi cắt wafer, chip là đầu ra quan trọng của quy trình sản xuất chất bán dẫn và các giai đoạn đóng gói và lưu trữ của chúng cũng quan trọng không kém. Các biện pháp đóng gói và lưu trữ phù hợp không chỉ cần thiết để đảm bảo tính an toàn và ổn định của chip trong quá trình vận chuyển và lưu trữ mà còn hỗ trợ mạnh mẽ cho các giai đoạn sản xuất, thử nghiệm và đóng gói tiếp theo.
Tóm tắt các giai đoạn kiểm tra và thử nghiệm:
Các bước kiểm tra và thử nghiệm chip sau khi cắt wafer bao gồm nhiều khía cạnh, bao gồm kiểm tra trực quan, đo kích thước, kiểm tra hiệu suất điện, kiểm tra chức năng, kiểm tra độ tin cậy và kiểm tra khả năng tương thích. Các bước này được kết nối và bổ sung cho nhau, tạo thành một rào cản vững chắc để đảm bảo chất lượng và độ tin cậy của sản phẩm. Thông qua các quy trình kiểm tra và thử nghiệm nghiêm ngặt, các vấn đề tiềm ẩn có thể được xác định và giải quyết kịp thời, đảm bảo sản phẩm cuối cùng đáp ứng các yêu cầu và kỳ vọng của khách hàng.
Diện mạo | Nội dung |
Biện pháp đóng gói | 1.Chống tĩnh điện:Vật liệu đóng gói phải có khả năng chống tĩnh điện tuyệt vời để ngăn chặn tĩnh điện làm hỏng thiết bị hoặc ảnh hưởng đến hiệu suất của thiết bị. |
2.Chống ẩm:Vật liệu đóng gói phải có khả năng chống ẩm tốt để tránh bị ăn mòn và suy giảm hiệu suất điện do độ ẩm gây ra. | |
3.Chống sốc:Vật liệu đóng gói phải có khả năng hấp thụ sốc hiệu quả để bảo vệ chip khỏi rung động và va đập trong quá trình vận chuyển. | |
Môi trường lưu trữ | 1.Kiểm soát độ ẩm: Kiểm soát chặt chẽ độ ẩm trong phạm vi thích hợp để ngăn ngừa sự hấp thụ độ ẩm và ăn mòn do độ ẩm quá cao hoặc các vấn đề tĩnh điện do độ ẩm thấp. |
2.Sự sạch sẽ: Duy trì môi trường lưu trữ sạch sẽ để tránh bụi và tạp chất làm nhiễm bẩn chip. | |
3.Kiểm soát nhiệt độ: Đặt phạm vi nhiệt độ hợp lý và duy trì nhiệt độ ổn định để ngăn ngừa hiện tượng lão hóa nhanh do nhiệt độ quá cao hoặc các vấn đề ngưng tụ do nhiệt độ thấp gây ra. | |
Kiểm tra thường xuyên | Kiểm tra và đánh giá chip lưu trữ thường xuyên, sử dụng các biện pháp kiểm tra trực quan, đo kích thước và thử nghiệm hiệu suất điện để xác định và giải quyết các vấn đề tiềm ẩn kịp thời. Dựa trên thời gian và điều kiện lưu trữ, hãy lập kế hoạch sử dụng chip để đảm bảo chúng được sử dụng trong điều kiện tối ưu. |
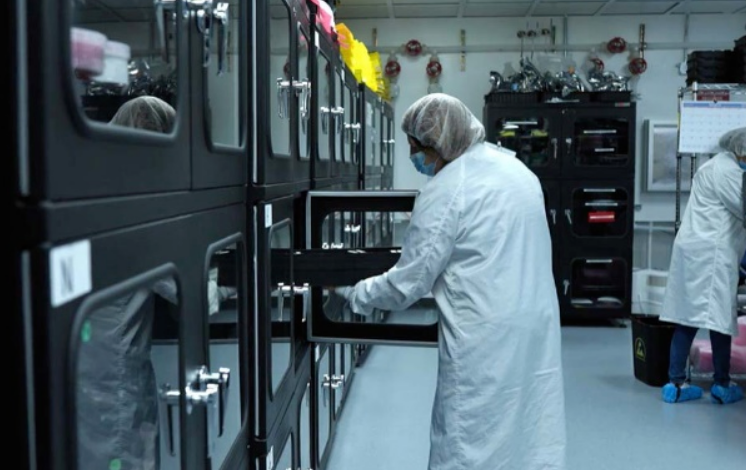
Vấn đề về các vết nứt nhỏ và hư hỏng trong quá trình cắt wafer là một thách thức đáng kể trong sản xuất chất bán dẫn. Ứng suất cắt là nguyên nhân chính gây ra hiện tượng này, vì nó tạo ra các vết nứt nhỏ và hư hỏng trên bề mặt wafer, dẫn đến tăng chi phí sản xuất và giảm chất lượng sản phẩm.
Để giải quyết thách thức này, điều quan trọng là phải giảm thiểu ứng suất cắt và triển khai các kỹ thuật, công cụ và điều kiện cắt được tối ưu hóa. Việc chú ý cẩn thận đến các yếu tố như vật liệu lưỡi cắt, tốc độ cắt, áp suất và phương pháp làm mát có thể giúp giảm sự hình thành các vết nứt nhỏ và cải thiện năng suất chung của quy trình. Ngoài ra, nghiên cứu đang diễn ra về các công nghệ cắt tiên tiến hơn, chẳng hạn như cắt bằng tia laser, đang khám phá các cách để giảm thiểu hơn nữa các vấn đề này.
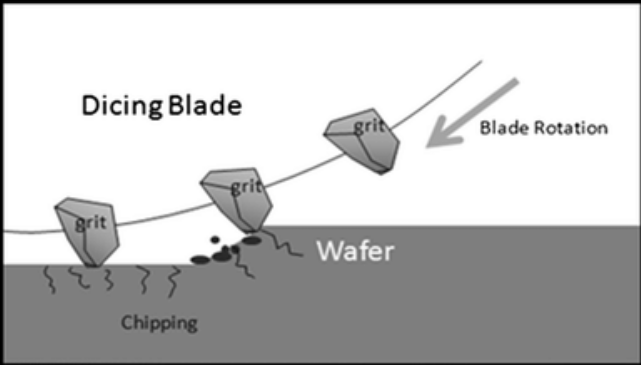
Là một vật liệu dễ vỡ, wafer dễ bị thay đổi cấu trúc bên trong khi chịu ứng suất cơ học, nhiệt hoặc hóa học, dẫn đến hình thành các vết nứt nhỏ. Mặc dù các vết nứt này có thể không dễ nhận thấy ngay lập tức, nhưng chúng có thể mở rộng và gây ra thiệt hại nghiêm trọng hơn khi quá trình sản xuất diễn ra. Vấn đề này trở nên đặc biệt khó khăn trong các giai đoạn đóng gói và thử nghiệm tiếp theo, khi nhiệt độ dao động và ứng suất cơ học bổ sung có thể khiến các vết nứt nhỏ này phát triển thành các vết nứt có thể nhìn thấy, có khả năng dẫn đến hỏng chip.
Để giảm thiểu rủi ro này, điều cần thiết là phải kiểm soát quá trình cắt cẩn thận bằng cách tối ưu hóa các thông số như tốc độ cắt, áp suất và nhiệt độ. Sử dụng các phương pháp cắt ít gây hại hơn, chẳng hạn như cắt bằng tia laser, có thể giảm ứng suất cơ học trên wafer và giảm thiểu sự hình thành các vết nứt nhỏ. Ngoài ra, việc triển khai các phương pháp kiểm tra tiên tiến như quét hồng ngoại hoặc chụp X-quang trong quá trình cắt wafer có thể giúp phát hiện các vết nứt ở giai đoạn đầu này trước khi chúng gây ra thiệt hại thêm.
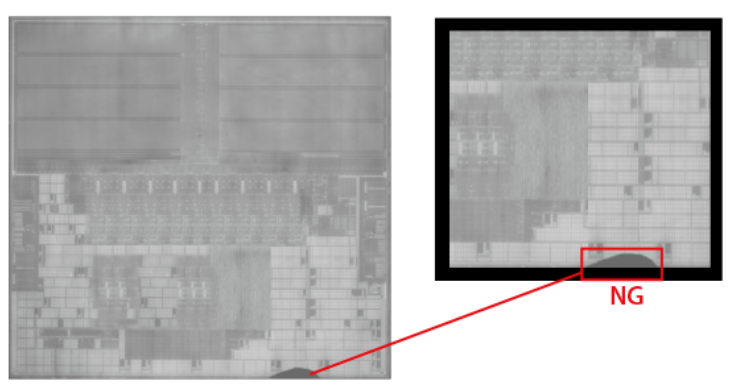
Thiệt hại trên bề mặt wafer là mối quan tâm đáng kể trong quá trình cắt, vì nó có thể ảnh hưởng trực tiếp đến hiệu suất và độ tin cậy của chip. Thiệt hại như vậy có thể do sử dụng không đúng công cụ cắt, thông số cắt không chính xác hoặc khuyết tật vật liệu vốn có trong chính wafer. Bất kể nguyên nhân là gì, những thiệt hại này có thể dẫn đến thay đổi điện trở hoặc điện dung của mạch, ảnh hưởng đến hiệu suất chung.
Để giải quyết những vấn đề này, hai chiến lược chính đang được nghiên cứu:
1. Tối ưu hóa các thông số và công cụ cắt:Bằng cách sử dụng lưỡi dao sắc hơn, điều chỉnh tốc độ cắt và thay đổi độ sâu cắt, có thể giảm thiểu sự tập trung ứng suất trong quá trình cắt, do đó giảm khả năng hư hỏng.
2. Khám phá công nghệ cắt mới: Các kỹ thuật tiên tiến như cắt laser và cắt plasma mang lại độ chính xác được cải thiện đồng thời có khả năng giảm mức độ hư hỏng gây ra cho wafer. Các công nghệ này đang được nghiên cứu để tìm ra cách đạt được độ chính xác cắt cao đồng thời giảm thiểu ứng suất nhiệt và cơ học trên wafer.
Diện tích tác động nhiệt và ảnh hưởng của nó đến hiệu suất
Trong các quy trình cắt nhiệt như cắt laser và cắt plasma, nhiệt độ cao chắc chắn sẽ tạo ra vùng tác động nhiệt trên bề mặt wafer. Khu vực này, nơi có độ dốc nhiệt độ đáng kể, có thể làm thay đổi các đặc tính của vật liệu, ảnh hưởng đến hiệu suất cuối cùng của chip.
Tác động của Vùng ảnh hưởng nhiệt (TAZ):
Thay đổi cấu trúc tinh thể: Ở nhiệt độ cao, các nguyên tử bên trong vật liệu wafer có thể sắp xếp lại, gây ra sự biến dạng trong cấu trúc tinh thể. Sự biến dạng này làm yếu vật liệu, làm giảm độ bền cơ học và độ ổn định của vật liệu, làm tăng nguy cơ hỏng chip trong quá trình sử dụng.
Những thay đổi trong tính chất điện: Nhiệt độ cao có thể làm thay đổi nồng độ chất mang và tính di động trong vật liệu bán dẫn, ảnh hưởng đến độ dẫn điện và hiệu suất truyền dòng điện của chip. Những thay đổi này có thể làm giảm hiệu suất của chip, có khả năng khiến chip không phù hợp với mục đích sử dụng dự kiến.
Để giảm thiểu những tác động này, việc kiểm soát nhiệt độ trong quá trình cắt, tối ưu hóa các thông số cắt và khám phá các phương pháp như tia làm mát hoặc xử lý sau xử lý là những chiến lược thiết yếu để giảm mức độ tác động nhiệt và duy trì tính toàn vẹn của vật liệu.
Nhìn chung, cả vết nứt nhỏ và vùng va chạm nhiệt đều là những thách thức quan trọng trong công nghệ cắt wafer. Cần tiếp tục nghiên cứu, cùng với những tiến bộ công nghệ và các biện pháp kiểm soát chất lượng, để cải thiện chất lượng sản phẩm bán dẫn và tăng cường khả năng cạnh tranh trên thị trường.
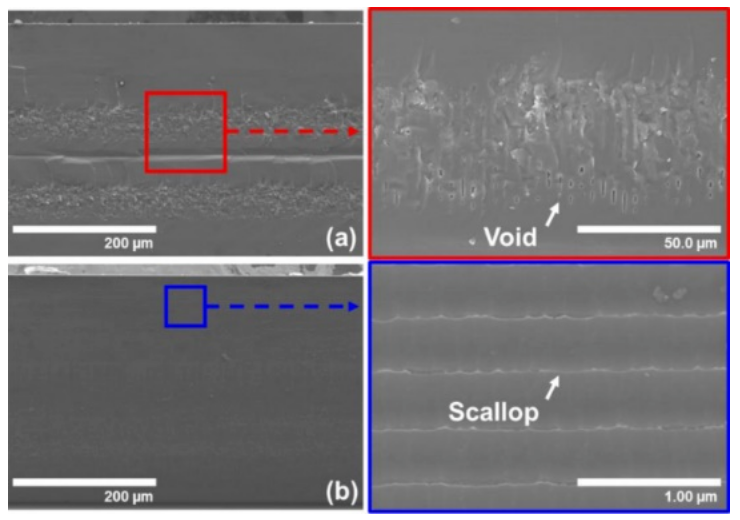
Các biện pháp kiểm soát vùng tác động nhiệt:
Tối ưu hóa các thông số quy trình cắt: Giảm tốc độ cắt và công suất có thể giảm thiểu hiệu quả kích thước của vùng tác động nhiệt (TAZ). Điều này giúp kiểm soát lượng nhiệt sinh ra trong quá trình cắt, tác động trực tiếp đến các đặc tính vật liệu của wafer.
Công nghệ làm mát tiên tiến: Việc áp dụng các công nghệ như làm mát bằng nitơ lỏng và làm mát bằng vi lưu chất có thể hạn chế đáng kể phạm vi của vùng tác động nhiệt. Các phương pháp làm mát này giúp tản nhiệt hiệu quả hơn, do đó bảo toàn các đặc tính vật liệu của wafer và giảm thiểu thiệt hại do nhiệt.
Lựa chọn vật liệu:Các nhà nghiên cứu đang khám phá các vật liệu mới, chẳng hạn như ống nano carbon và graphene, có độ dẫn nhiệt và độ bền cơ học tuyệt vời. Những vật liệu này có thể giảm vùng tác động nhiệt đồng thời cải thiện hiệu suất chung của chip.
Tóm lại, mặc dù vùng tác động nhiệt là hậu quả tất yếu của công nghệ cắt nhiệt, nhưng nó có thể được kiểm soát hiệu quả thông qua các kỹ thuật xử lý được tối ưu hóa và lựa chọn vật liệu. Nghiên cứu trong tương lai có thể sẽ tập trung vào việc tinh chỉnh và tự động hóa các quy trình cắt nhiệt để đạt được hiệu quả và độ chính xác cao hơn trong việc cắt lát wafer.

Chiến lược cân bằng:
Đạt được sự cân bằng tối ưu giữa năng suất wafer và hiệu quả sản xuất là một thách thức liên tục trong công nghệ cắt wafer. Các nhà sản xuất cần xem xét nhiều yếu tố, chẳng hạn như nhu cầu thị trường, chi phí sản xuất và chất lượng sản phẩm, để phát triển chiến lược sản xuất hợp lý và các thông số quy trình. Đồng thời, việc đưa vào sử dụng thiết bị cắt tiên tiến, cải thiện kỹ năng của người vận hành và tăng cường kiểm soát chất lượng nguyên liệu thô là điều cần thiết để duy trì hoặc thậm chí cải thiện năng suất trong khi tăng hiệu quả sản xuất.
Thách thức và cơ hội trong tương lai:
Với sự tiến bộ của công nghệ bán dẫn, việc cắt wafer phải đối mặt với những thách thức và cơ hội mới. Khi kích thước chip thu hẹp và tích hợp tăng lên, nhu cầu về độ chính xác và chất lượng cắt tăng lên đáng kể. Đồng thời, các công nghệ mới nổi cung cấp những ý tưởng mới cho việc phát triển các kỹ thuật cắt wafer. Các nhà sản xuất phải luôn theo kịp động lực thị trường và xu hướng công nghệ, liên tục điều chỉnh và tối ưu hóa các chiến lược sản xuất và thông số quy trình để đáp ứng những thay đổi của thị trường và nhu cầu công nghệ.
Tóm lại, bằng cách kết hợp các cân nhắc về nhu cầu thị trường, chi phí sản xuất và chất lượng sản phẩm, đồng thời giới thiệu thiết bị và công nghệ tiên tiến, nâng cao kỹ năng của người vận hành và tăng cường kiểm soát nguyên liệu thô, các nhà sản xuất có thể đạt được sự cân bằng tốt nhất giữa sản lượng wafer và hiệu quả sản xuất trong quá trình cắt wafer, dẫn đến sản xuất sản phẩm bán dẫn hiệu quả và chất lượng cao.
Triển vọng tương lai:
Với những tiến bộ công nghệ nhanh chóng, công nghệ bán dẫn đang tiến triển với tốc độ chưa từng có. Là một bước quan trọng trong sản xuất bán dẫn, công nghệ cắt wafer đang sẵn sàng cho những phát triển mới thú vị. Nhìn về phía trước, công nghệ cắt wafer dự kiến sẽ đạt được những cải tiến đáng kể về độ chính xác, hiệu quả và chi phí, mang lại sức sống mới cho sự tăng trưởng liên tục của ngành công nghiệp bán dẫn.
Tăng độ chính xác:
Trong quá trình theo đuổi độ chính xác cao hơn, công nghệ cắt wafer sẽ liên tục đẩy giới hạn của các quy trình hiện có. Bằng cách nghiên cứu sâu các cơ chế vật lý và hóa học của quy trình cắt và kiểm soát chính xác các thông số cắt, kết quả cắt mịn hơn sẽ đạt được để đáp ứng các yêu cầu thiết kế mạch ngày càng phức tạp. Ngoài ra, việc khám phá các vật liệu và phương pháp cắt mới sẽ cải thiện đáng kể năng suất và chất lượng.
Nâng cao hiệu quả:
Thiết bị cắt wafer mới sẽ tập trung vào thiết kế thông minh và tự động. Việc đưa vào các hệ thống điều khiển và thuật toán tiên tiến sẽ cho phép thiết bị tự động điều chỉnh các thông số cắt để phù hợp với các vật liệu và yêu cầu thiết kế khác nhau, do đó cải thiện đáng kể hiệu quả sản xuất. Những cải tiến như công nghệ cắt nhiều wafer và hệ thống thay thế lưỡi dao nhanh sẽ đóng vai trò quan trọng trong việc nâng cao hiệu quả.
Giảm chi phí:
Giảm chi phí là hướng đi chính cho sự phát triển của công nghệ cắt wafer. Khi vật liệu và phương pháp cắt mới được phát triển, chi phí thiết bị và chi phí bảo trì dự kiến sẽ được kiểm soát hiệu quả. Ngoài ra, việc tối ưu hóa quy trình sản xuất và giảm tỷ lệ phế liệu sẽ tiếp tục giảm chất thải trong quá trình sản xuất, dẫn đến giảm tổng chi phí sản xuất.
Sản xuất thông minh và IoT:
Sự tích hợp của công nghệ sản xuất thông minh và Internet vạn vật (IoT) sẽ mang lại những thay đổi mang tính chuyển đổi cho công nghệ cắt wafer. Thông qua khả năng kết nối và chia sẻ dữ liệu giữa các thiết bị, mọi bước của quy trình sản xuất đều có thể được giám sát và tối ưu hóa theo thời gian thực. Điều này không chỉ cải thiện hiệu quả sản xuất và chất lượng sản phẩm mà còn cung cấp cho các công ty khả năng dự báo thị trường và hỗ trợ ra quyết định chính xác hơn.
Trong tương lai, công nghệ cắt wafer sẽ có những tiến bộ đáng kể về độ chính xác, hiệu quả và chi phí. Những tiến bộ này sẽ thúc đẩy sự phát triển liên tục của ngành công nghiệp bán dẫn và mang lại nhiều cải tiến công nghệ và tiện ích hơn cho xã hội loài người.
Thời gian đăng: 19-11-2024